"All of the options were there, but not on the same bike": Carbon Wasp's founder talks UK manufacturing, the rise of the gearbox, and building mountain bikes for British riders
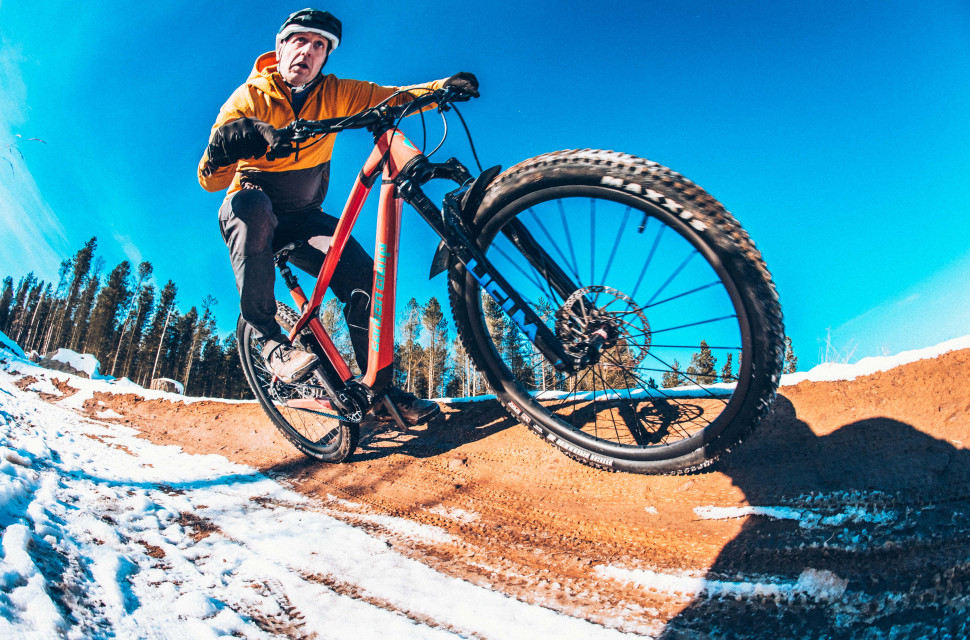
Although Carbon Wasp initially established itself by creating carbon fibre arm rests for time trial cyclists and triathletes, the brand has always had mountain biking at its very core. Over the past couple of years, the Yorkshire-based innovator has been producing handmade carbon mountain bikes, unveiling model after model while bringing something rather unique to the carbon frame market: customisation options. We caught up with Adrian Smith, founder of Carbon Wasp, to learn more about how the brand came to be, carbon fibre manufacturing in the UK and gearboxes.
- Carbon Wasp Carbon Gearbox Hardtail first ride review
- Carbon Wasp expands range with the Compound-150 trail bike
- We talk with Starling Cycles about thermoplastic carbon
Carbon Wasp is a small UK-based brand that’s doing something very different to what others of a similar size are up to - hand-laying carbon fibre frames. With such bikes usually being built in Taiwan, the move to do so on home soil is certainly one that raises eyebrows. However, it’s brought some serious expertise and uniqueness to the UK market, where most small-batch manufacturers produce top-notch steel alternatives.
The result of being a small brand with some serious carbon know-how is manoeuvrability in the market, with the employment of gearboxes seemingly being the next step for the brand. Here’s what Adrian had to say after I went for a spin on the brand’s Carbon Gearbox Hardtail.
off.road.cc: What’s the story behind Carbon Wasp?
Adrian Smith: It’s a classic tale of there not being a bike around at the time that had everything I wanted on it, so I set out to build a bike that I wanted. Unfortunately, the cost of building bikes out of aluminium ended up costing a fortune just to do the machining as one-offs. I kept having ideas and I wanted to realise them and, as I say, it became prohibitive to do it in metal.
So the difficulty with carbon fibre is that the process itself is very crude and simple on one level, but the difficulty is always forming shapes in moulds, so you need something to give the carbon its shape, which can be a very expensive machined metal part, but the first frame I made was based on a foam core that I shaped by hand with a sanding block. I wire cut a 2D profile out of two halves and bonded them together, and then hand-shaped it into round tubes, so you get the alignment from two halves. So it’s really basic.
A step up from that was 3D printing, which was something a friend put me onto, and it was cheaper than working with metal, so I ended up learning how to print plastic moulds, which then brought complications with temperature and pressure to get something strong enough. I ended up making a big 3D printer that printed polycarbonate, which can go strong and can withstand high temperatures. That’s how it started.
Once I had done that, I had the capability to make bike frame-sized moulds. They were pure one-offs as the moulds usually broke during demoulding. But it was quite good fun and accessible, so I did the printing in my garage, and the crude layup could be done anywhere.
So we were getting some fairly good results, but the finish wasn’t great because the printing process wasn’t ideal, but that’s how it started. I was just making bikes and parts for myself, and people started asking me to make bits for them.
Then, in the early days, we started making custom projects for people, which often didn’t work because what we were really doing was prototyping for existing companies. There were also a few individuals who just wanted something a bit weird that they couldn’t buy. It was worthwhile, but it’s got some significant drawbacks because everything I built was a prototype.
What I always wanted to do was settle on a design and then refine that, rather than always doing random things, and that’s how Carbon Wasp came about. We were starting to get money in from repairs and projects. I then thought we would put it through a company to make it official and get a workshop. It just sort of grew from there.
We’ve now got a set-up where we’ve got a mini factory with fairly traditional methods using pre-pregs, autoclaves and metal tooling, and we make proper stuff, hopefully.
orcc: When you started the business, was there something about the bikes on offer at the time that inspired your design?
AS: I was thinking about this recently, actually. It’s hard to remember and pinpoint what it was, but there were definitely a sense that I couldn’t buy the bike I wanted... I think what it was, is that I could buy bikes with all of the features I did want, so geometry, sizing, storage, you know... all of the options were there, but not on the same bike.
All I really did was collect them up into one thing. All of the bikes I designed back then, I don’t think any of them were groundbreaking, as everything on the bikes was available already, just not in the same place. And I think that’s what it was that made me want to do it.
orcc: What of that inspiration can you see in Carbon Wasp’s current bikes?
AS: I suppose it’s the same sort of thing we’ve got. Because we are low volume and we can turn things around fairly quickly, we can be quite responsive and adapt. The bikes we make are really for the style of riding that we have in the UK. So the woods, some pretty technical descents where things get out of hand quite quickly, but at the same time, you get to the bottom and you’ve got to get yourself back to the top. So it’s about that all-around bike.
What I thought, and still think, when I developed the Truffle-120, for example, was that a 140/150mm [travel] bike was a bit much for what I was doing, and an aggressive 120 was spot on. That coincided with the release of the RockShox SID fork and the tyres and everything that’s evolved alongside it. So I think that for the last few years now, I think it’s been possible to put together this really capable 120mm bike that probably wouldn’t have been thought about before.
I suppose that, drawing on the past, it’s putting that together, block by block, what it is that we want from our bikes. So you know, short travel but robust with storage, with progressive geometry and with adjustability - although our bikes aren’t adjustable, rather, there are options. So we do a range of chainstay lengths - it’s not an adjustment, but it’s an option that you choose and can swap out, but we don’t use flip chips. But it gives you that range, and a lot of that stuff comes to personal preference.
People have different views, so we can make different options. Equally, how you set up the bike is important, so things like tyre choice and the fork you’re running. Everyone has an idea of where they want to pitch their bike, and everything leads towards that. Are you compromising grip for weight? Or the other way around. And then a frame is just part of the puzzle, and our goal is to make them sort of neutral in the way that you can set them up in a way that suits what you want to do.
orcc: Do you think being a smaller brand gives you an advantage over others?
AS: I’d like to think so, but sometimes there are definite drawbacks in terms of awareness and the whole infrastructure of supply and distribution of bikes. I can definitely see the advantage of having a huge machine and going along with that. But we are a tiny business in terms of a corporate identity, so a customer can call in to order a bike, and they would probably speak to me. If you speak to me later in the day, I would be laying up someone else's frame, and so for some people, there’s a lot of value there.
What I would say is that it does bring a benefit in the way that if you phone up and have a clear idea of what you want, or if you’re unsure, we can tailor what we do to what someone needs. And that customer can come and pick up their bike, and they can see the process, how it’s been done and where it’s been done.
The advantage is that we are the people who design, test and ride the bike as well as the people who make them. We’re also the people who would sell you the bike, so there’s a level of connection and immediacy.
In terms of customisation, that brings a benefit, but also in understanding the product.
orcc: We’re seeing Pinion gearboxes on your bikes, why is that, and do you think it’s the future?
AS: I’ve been working on gearbox bikes for years, since something like 2006, when there was a Eurobike where gearboxes were everywhere. Back then, I was really interested in gearboxes, and I designed one, but it wasn’t quite as good as the Pinion ones, so I shelved those plans.
I had an interest in gearboxes since then, and a few years ago we built some carbon frames for another brand - a hardtail, which was interesting - they stopped doing those and started building them in metal, so I always wanted to carry that on. It was always a plan that we would make some kind of gearbox bike.
I think there are certain use cases in which the advantages really come into the fore, and for me, that’s the gravity side, which we’ve seen on the downhill bikes, and that makes total sense because of the weight. It also makes sense on a winter hardtail because of the durability and basically zero maintenance due to the belt drive. I’ve always thought there are real advantages for those, but maybe not so much in the middle, the sort of trail bike. But a lot of people have spoken to me and disagree.
There have been some developments in gearboxes in that the shifting has changed with a trigger shift and the auto shift function, which I think is great. Maybe not for every type of riding, but for certain types it’s good. Just the way of shifting is quicker and simpler. Before, it was always a cable-operated twist shift, which was quirky, I thought.
And then weight. We’re perhaps less obsessed with weight, and if you’re putting a gearbox on a reasonably lightweight carbon frame and you can build it up with decent componentry, you can make the overall bike reasonably light, but you can still play on those advantages.
orcc: So you’re seeing a demand for gearbox bikes?
AS: Absolutely, and definitely moreso. This might coincide with us launching new bikes, so we’re getting more attention and more feedback because of that. But I’ve definitely noticed an increase in interest in gearboxes, especially since all of the downhill stuff has come out over the winter.
We’re now making a Truffle-120 with a gearbox, which I think could actually be a good solution. This time last year, I would have said no chance - there are better ways to use the gearbox, but I think that trail bike use is feasible.
I don’t know if it is the future, but it is definitely a future. Everything in future is e-bikes, isn’t it? Or gravel bikes, depending on who you ask.
It’s got the potential to be hugely beneficial, but it does need a lot of development. Although Pinion and Effigear are producing well-refined components, they perhaps need one of the bigger brands to bring some competition and to bring a gearbox that’s more relevant to trail use.
orcc: What’s next for Carbon Wasp?
AS: So we’ve got a gravel bike that we’re working on now that’ll be coming out very soon. We’ll have that in the next few weeks, I hope. That’ll be a BSA bottom bracket and a Pinion gearbox [options]. We’ll then be doing a Pinion Truffle-120 and we’ve got another 150 frame that we make, so I wouldn’t be surprised to see a gearbox on one of them eventually.
And then aside from that, we’ve got other little projects going on. It would be good to have someone making carbon rims in Yorkshire, wouldn’t it?